24 Oct 2023
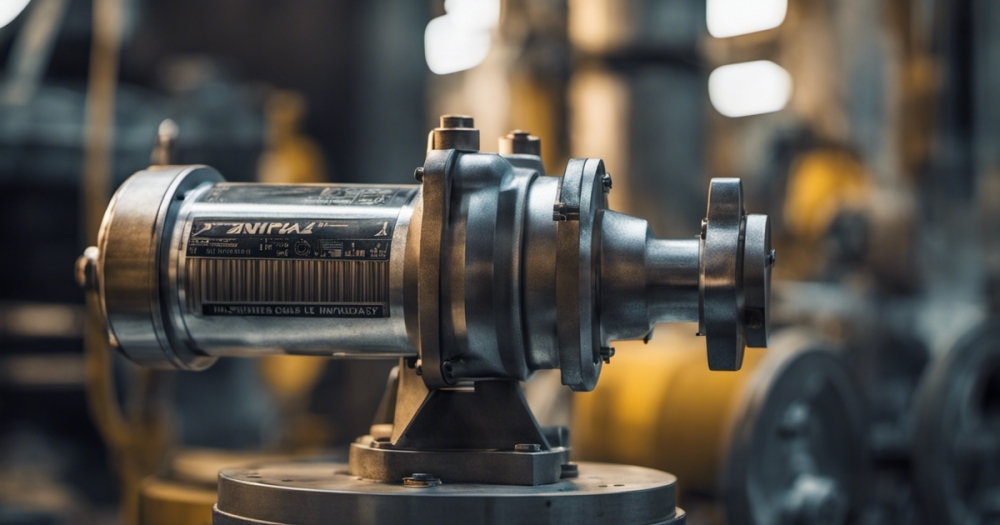
Centrifugal Pumps: Types, Applications, and Benefits
Centrifugal Pumps: Types, Applications, and Benefits
Looking to move fluids efficiently and reliably? Want to know about an essential piece of equipment used in various industries for fluid transportation? Look no further than vertical pumps, submersible pumps, and jet pumps. These pumps are crucial for a wide range of pumping applications. Have you ever wondered how fluids are transported in industries such as water supply, wastewater treatment, and chemical processing using vertical pumps and submersible pumps for various pumping applications and flows? Or how heating and cooling systems work in HVAC applications to minimize energy costs? This includes the use of vertical pumps and jet pumps to efficiently circulate fluids. Understanding the actual pump used in the system is crucial for optimizing its performance.
Centrifugal pumps are the answer. These powerful vertical pumps and positive displacement pumps convert mechanical energy into kinetic energy, propelling fluids through pipelines with ease. With their multiple impellers, these pumps ensure high pumping efficiency. Trash pumps are essential for transporting fluids and facilitating the flow in various applications. They are used for circulating water, transferring chemicals, and can have multiple impellers. With different impeller diameters and designs available, centrifugal pumps can be tailored to meet specific pumping efficiency needs in a piping system.
In this article, we'll explore the working principles of the motor product, its applications across industries, and the various components that make it tick. So buckle up as we embark on a journey to uncover the ins and outs of centrifugal pumps, including their suction capabilities, motor functionality, and the casing that houses them.
How Centrifugal Pumps Work
Centrifugal pumps, powered by a motor, are widely used in various industries for their ability to create suction and transfer fluids through the shaft. This reliable and versatile product is an essential component in many industrial processes. Positive displacement pumps and trash pumps rely on the centrifugal force generated by a rotating impeller to move fluids from one place to another. The pump head and suction are crucial in this process. Let's take a closer look at how these well pumps work. These pumps use a product that is inserted into the shaft. In this article, we will explore the mechanics of these pumps.
Relies on the centrifugal force generated by a rotating impeller
At the heart of a centrifugal pump is an impeller, which is typically made up of curved blades or vanes. This article discusses the positive displacement pumps, their shaft, and the product they transfer. The impeller of positive displacement pumps rotates rapidly, creating a centrifugal force that pushes the fluid outward, increasing the pump head. The rotation is facilitated by the shaft, ensuring efficient movement of the product. This force is what allows positive displacement pumps to efficiently move liquids through the shaft and create head.
Fluid enters through the center of the impeller and is accelerated outward
When the pump is running, fluid enters through the center of the impeller shaft and flows towards the head. As the pump head impeller spins, it accelerates the incoming fluid, increasing its velocity along the shaft. This acceleration occurs due to the shape and design of the impeller blades, which create a sort of "whirling" effect around the pump head and shaft.
The high-speed fluid is then redirected by the pump casing towards the outlet
Once accelerated, the high-speed fluid moves towards the outer edge of the impeller shaft and into a surrounding pump casing or volute head. The casing, along with the pump head, acts as a guide for directing and redirecting the flow of fluid towards its desired destination—typically, an outlet pipe or system. The shaft ensures smooth operation of the pump.
Kinetic energy is converted back into pressure as fluid exits the pump
As fluid leaves the spinning impeller and moves through narrow passages within the casing, its kinetic energy starts transforming back into pressure energy, increasing the pump head. This transformation occurs as the fluid passes through the shaft. This conversion happens because of changes in flow direction and velocity reduction within the pump head and shaft passages.
The resulting increase in pressure allows for efficient movement of the pump head against resistance or elevation differences in piping systems. The pump head is connected to the shaft, which facilitates this movement. In other words, the pump head helps push fluids uphill or overcome any obstacles they may encounter along their path by utilizing the shaft.
Efficiency depends on factors like impeller design, speed, and system conditions
The efficiency of a centrifugal pump relies on several factors, including the shaft. One crucial factor in the design of the impeller itself is the pump head and shaft. Different impeller designs can impact how effectively the pump moves fluid and converts mechanical energy into pressure. The design of the shaft also plays a crucial role in this process.
The speed at which the pump head and shaft impeller rotates also affects efficiency. Higher speeds generally result in greater fluid flow rates and can also increase energy consumption due to the pump head and shaft. The specific conditions of the system, such as temperature, viscosity, pressure requirements, pump head, and shaft, also play a role in determining overall efficiency.
Centrifugal pumps, with their rotating shaft, offer several advantages over other types of pumps, such as magnetic drive pumps or positive displacement pumps.
- They can handle large volumes of fluids efficiently.
- They are generally more cost-effective for high-flow applications, especially when considering the pump head.
- They have fewer moving parts, reducing maintenance needs.
- They can operate at higher speeds for increased flow rates.
However, they do have some limitations:
- They may not be suitable for handling highly viscous liquids.
- They may experience reduced efficiency at lower flow rates.
- They require careful consideration of system conditions to ensure optimal performance.
Types of Centrifugal Pumps
Centrifugal pumps come in various types, each designed to suit different applications and operating conditions. Let's explore the different types of centrifugal pumps and their unique characteristics.
Single-stage pumps
Single-stage pumps are the simplest type of centrifugal pump. They feature a single impeller that rotates within the pump casing to create pressure and move fluid. These pumps are commonly used for low-pressure applications where a moderate flow rate is required.
Pros:
- Simple design with fewer components, making them easy to maintain
- Cost-effective option for applications with low-pressure requirements
Cons:
- Limited ability to handle high pressures
- Lower efficiency compared to multi-stage pumps for high-head applications
Multi-stage pumps
Multi-stage pumps consist of multiple impellers arranged in series within the pump casing. Each impeller adds energy to the fluid, allowing for higher pressure generation. These pumps are ideal for applications that require higher pressures or pumping fluids over long distances.
Pros:
- Ability to generate higher pressures than single-stage pumps
- Suitable for applications requiring high head or long-distance pumping
Cons:
- More complex design with multiple impellers, resulting in increased maintenance requirements
- Higher initial cost compared to single-stage pumps
Axial flow pumps
Axial flow pumps are designed for large volume transfer, where the fluid flows parallel to the shaft axis. These pumps feature an impeller with curved blades that push the fluid in a linear direction along the shaft axis. They are commonly used in flood control systems, irrigation, and wastewater treatment plants.
Pros:
- Efficient at moving large volumes of fluid
- Ideal for low-head, high-flow rate applications
Cons:
- Limited ability to generate high pressures
- Not suitable for applications requiring significant pressure differences between inlet and outlet points
Radial flow pumps
Radial flow pumps move fluid perpendicular to the shaft axis. The impeller in these pumps pushes the fluid outward from the center of rotation, creating pressure. These pumps are commonly used for medium-pressure applications such as water supply systems and HVAC (Heating, Ventilation, and Air Conditioning) systems.
Pros:
- Ability to handle moderate pressures
- Versatile option suitable for various applications
Cons:
- Lower efficiency compared to axial flow pumps for high-flow rate applications
- Limited ability to handle extremely high pressures
Mixed flow pumps
Mixed flow pumps combine both axial and radial flow characteristics. The impeller design allows fluid to move both axially and radially, resulting in a combination of high flow rates and moderate pressures. These pumps are commonly used in agricultural irrigation systems, cooling towers, and large-scale industrial applications.
Types and Applications of Centrifugal Pumps
Centrifugal pumps are widely used in various pumping applications due to their efficiency and reliability. Let's explore the different types of centrifugal pumps and their specific applications.
End Suction Pumps
End suction pumps are commonly used for general water transfer applications. These pumps feature a single impeller that draws water from one end and discharges it from the other. They are versatile and can handle a wide range of liquids, making them suitable for both agricultural and domestic applications.
Pros:
- Easy installation and maintenance
- Compact design, saving space
- Cost-effective option for water transfer tasks
Cons:
- Limited to low-to-medium pressure tasks
- Not suitable for high-flow or high-viscosity fluids
Split Case Pumps
Split case pumps are ideal for high-flow, low-to-medium pressure tasks. As the name suggests, these pumps have a split casing which allows easy access to the internal components for maintenance or repairs. They are commonly used in industrial settings where large volumes of liquid need to be moved efficiently.
Pros:
- High efficiency and performance
- Can handle large flow rates
- Easy access to internal components for maintenance
Cons:
- Requires more space due to larger size
- Higher initial cost compared to end suction pumps
Vertical Turbine Pumps
Vertical turbine pumps are specifically designed for deep well or sump pumping operations. These pumps consist of multiple stages with impellers stacked on top of each other, allowing them to pump water from great depths. They are commonly used in agriculture, mining, and municipal water supply systems.
Pros:
- Can pump water from deep wells or sumps
- Space-saving design as they can be installed vertically
- Suitable for high-head applications
Cons:
- Complex installation process
- Higher maintenance requirements compared to other types of centrifugal pumps
Submersible Pumps
Submersible pumps are designed to operate underwater, making them suitable for applications where the pump needs to be submerged in the liquid being pumped. They are often used in sewage systems, drainage systems, and wastewater treatment plants.
Pros:
- Can handle solids and debris without clogging
- Quiet operation due to submerged design
- Requires less space as they can be installed directly in the liquid
Cons:
- Higher initial cost compared to other types of pumps
- Regular maintenance required to prevent damage from prolonged submersion
Diaphragm Pumps
Diaphragm pumps are used when handling abrasive or corrosive fluids. These pumps use a flexible diaphragm that moves back and forth, creating pressure variations that push the fluid through the pump. They are commonly used in industries such as chemical processing, mining, and oil and gas.
Advantages and Benefits of Centrifugal Pumps
Centrifugal pumps offer numerous advantages and benefits, making them a popular choice for various applications. Let's explore why these pumps are highly efficient, easy to install, and capable of handling different types of liquids.
Efficient operation with minimal maintenance requirements
Centrifugal pumps are known for their pumping efficiency, ensuring accurate flow rates while minimizing energy consumption. With their simple design and fewer moving parts compared to other pump types, they require minimal maintenance. This translates to cost savings in terms of both time and money.
- Efficiency: Centrifugal pumps operate at high speeds, allowing them to move fluids quickly and efficiently. This high velocity results in effective fluid transfer with minimal losses.
- Low maintenance: The simplicity of centrifugal pump designs means there are fewer components that can fail or require regular upkeep. This reduces downtime and maintenance costs.
Wide range of capacities and pressures available
One significant advantage of centrifugal pumps is the wide range of capacities and pressures they can handle. Whether you need a pump for low-flow applications or high-pressure systems, centrifugal pumps have got you covered.
- Versatility: Centrifugal pumps come in various sizes, allowing you to choose the one that suits your specific needs. From small-scale residential applications to large industrial projects, there is a centrifugal pump suitable for every requirement.
- Pressure capabilities: These pumps can handle both low-pressure and high-pressure systems effectively. They are designed to withstand the demands of different pressure ranges without compromising performance.
Simple installation process with compact designs
Installing a centrifugal pump is relatively straightforward due to its compact design and ease of integration into existing systems. Whether it's for residential or commercial use, you'll find that installing a centrifugal pump is hassle-free.
- Compact size: Centrifugal pumps have a compact footprint compared to other types of pumps. This makes them ideal for installations where space is limited.
- Easy integration: Centrifugal pumps can be easily integrated into existing piping systems, reducing the need for extensive modifications. This simplifies the installation process and saves time and effort.
Capable of handling various types of liquids including corrosive and abrasive fluids
Centrifugal pumps are versatileIncluding those that are corrosive or abrasive. This adaptability makes them suitable for a wide range of applications across various industries.
- Corrosive fluids: Centrifugal pumps can handle corrosive fluids by using materials such as stainless steel or specialized coatings that resist corrosion.
- Abrasive fluids: With their robust construction, centrifugal pumps can handle abrasive fluids without significant wear and tear. This ensures long-lasting performance even in demanding environments.
Ability to handle large volumes of fluid with high flow rates
One of the key advantages of centrifugal pumps is their ability to handle large volumes of fluid with high flow rates. This makes them ideal for applications where rapid fluid transfer is required.
- High flow rates: Centrifugal pumps operate at high speeds, enabling them to move large volumes of fluid quickly. This is particularly beneficial in scenarios where time is critical, such as firefighting or flood control.
- Efficient performance: The combination of high flow rates and efficient operation ensures that centrifugal pumps deliver optimal performance while minimizing energy consumption.
Criteria for Choosing Materials in Centrifugal Pumps
Choosing the right materials for centrifugal pumps is crucial to ensure their optimal performance and longevity. Several factors need to be considered when selecting materials for these pumps, including compatibility with the fluid being pumped, resistance to wear and erosion, operating conditions, cost-effectiveness, and compliance with industry standards and regulations. Let's delve into each of these criteria in more detail.
Compatibility with the Fluid Being Pumped
One of the primary considerations when choosing materials for centrifugal pumps is their compatibility with the fluid being pumped. Different fluids have varying chemical compositions and properties that can cause corrosion or degradation of certain materials. It is essential to select materials that are resistant to chemical reactions with the fluid to prevent damage or contamination.
Resistance to Wear, Erosion, and Cavitation
Centrifugal pumps often handle fluids that can be abrasive or corrosive in nature. The velocity of the fluid passing through the pump can cause wear on its internal components over time. To mitigate this issue, it is important to choose materials that have high resistance to wear, erosion, and cavitation caused by the fluid's properties.
Consideration of Temperature, Pressure, and Operating Conditions
The temperature, pressure, and operating conditions under which a centrifugal pump operates play a significant role in material selection. Different materials have different temperature limits beyond which they may degrade or lose their mechanical strength. Similarly, certain materials may not withstand high pressures or extreme operating conditions. It is crucial to choose materials that can withstand the specific temperature range, pressure levels, and other environmental factors associated with the pump's operation.
Cost-Effectiveness and Availability of Materials
Cost-effectiveness is an important factor when selecting materials for centrifugal pumps. Some materials may offer excellent chemical resistance but come at a higher cost compared to others. It is necessary to strike a balance between material performance and affordability without compromising on quality. The availability of materials should also be taken into consideration to ensure a smooth supply chain and minimize downtime in case of repairs or replacements.
Compliance with Industry Standards and Regulations
Centrifugal pumps are widely used in various industries, including oil and gas, chemical processing, water treatment, and more. Each industry has its own set of standards and regulations that govern the materials used in equipment like pumps. It is vital to choose materials that comply with these industry-specific standards to ensure safety, reliability, and compliance with legal requirements.
Common Problems and Troubleshooting with Centrifugal Pumps
Cavitation
Cavitation is a common problem that can occur in centrifugal pumps. It refers to the formation of vapor bubbles in the pump, which can lead to reduced pump performance. When these bubbles collapse, they create shockwaves that can cause damage to the impeller and other components of the pump. This can result in decreased flow rate, increased noise levels, and even complete failure of the pump. Cavitation is often caused by low pumping efficiency, high head pressure, or excessive head losses within the system.
Impeller Damage
Another major problem faced by centrifugal pumps is impeller damage. The impeller is a crucial component responsible for generating fluid flow within the pump. Over time, it may experience wear or become imbalanced due to factors such as erosion, corrosion, or cavitation. This can significantly impact the efficiency and flow rate of the pump. Damaged impellers may lead to reduced performance, increased energy consumption, and even complete failure of the pump if not addressed promptly.
Leakage
Leakage is a common issue encountered in centrifugal pumps and can have various causes. One frequent culprit is seal failure. Seals are used to prevent fluid from leaking out of the pump or contaminants from entering it. However, seals can deteriorate over time due to factors like wear and tear or improper installation. When seals fail, it results in fluid loss or contamination within the system. This not only affects pump performance but also poses safety risks and increases maintenance costs.
Motor Issues
Centrifugal pumps rely on motors for their operation, making motor issues another common challenge faced by users. Electrical faults such as motor burnout or short circuits can disrupt normal functioning and lead to pump failure. Mechanical failures like bearing wear or misalignment between the motor and pump shafts can also impact performance and cause premature breakdowns. Regular inspection and maintenance of the motor are essential to prevent such issues and ensure smooth pump operation.
Vibration and Noise
Vibration and noise are often indicators of underlying problems in centrifugal pumps. Excessive vibration can result from factors like imbalance, misalignment, or worn components. This not only affects pump performance but also poses risks to surrounding equipment and structures. Similarly, increased noise levels can be a sign of issues such as cavitation, impeller damage, or worn bearings. Monitoring vibration levels and addressing any abnormal noises promptly can help prevent further damage and extend the lifespan of the pump.
Leading Manufacturers and Suppliers of Centrifugal Pumps
There are several leading manufacturers and suppliers in the market. These companies offer a wide range of pumps for various applications, ensuring that industries across the globe have access to reliable pumping solutions. Let's take a closer look at some of these top players in the industry.
Grundfos: Renowned Global Supplier
Grundfos is a renowned global supplier that has been providing high-quality pumps for over 75 years. They offer a wide range of centrifugal pumps suitable for many industries, including water supply, power generation, and wastewater treatment. With their innovative designs and advanced technologies, Grundfos ensures efficient pumping solutions that meet the demands of modern industries.
- Pros:
- Wide variety of pump options available
- Innovative designs and advanced technologies
- Reliable and efficient pumping solutions
- Cons:
- Some models may be expensive compared to other brands
Sulzer Ltd.: Specialized Pump Solutions
Sulzer Ltd. specializes in centrifugal pumps designed specifically for industries such as oil & gas, water treatment, and power generation. With their expertise in rotating equipment and fluid dynamics, Sulzer delivers reliable pump solutions that can handle demanding applications. Their pumps are known for their durability, efficiency, and performance.
- Pros:
- Expertise in specialized pump solutions
- Durability and reliability
- High-performance pumps
- Cons:
- Limited options for other industries outside their specialization
KSB Group: Comprehensive Solutions Provider
KSB Group is another prominent player in the centrifugal pump market. They provide comprehensive solutions for industrial processes and building services across various industries. Whether it's supplying water to residential buildings or handling complex industrial processes, KSB offers a wide range of reliable pumps tailored to specific requirements.
- Pros:
- Comprehensive solutions for different industries
- Reliable and tailored pump options
- Extensive industry experience
- Cons:
- Some customers may find their pumps to be on the pricier side
Xylem Inc.: Innovative Water Management
Xylem Inc. is a leading provider of innovative pumping technologies for water management systems worldwide. Their centrifugal pumps are designed to efficiently handle water supply, wastewater treatment, irrigation, and other applications. With a focus on sustainability and energy efficiency, Xylem offers reliable pumping solutions that help conserve resources.
- Pros:
- Innovative pumping technologies
- Energy-efficient and sustainable solutions
- Wide range of pump options
- Cons:
- Limited presence in industries outside water management systems
Goulds Pumps (ITT): Established Manufacturer
Goulds Pumps, a subsidiary of ITT Corporation, is an established manufacturer known for its reliable centrifugal pumps. They offer a wide variety of pump models suitable for many industries, including water supply, power generation, chemical processing, and more. Goulds Pumps are known for their robust construction and long-lasting performance.
- Pros:
- Wide range of pump models available
- Robust construction for durability
- Long-lasting performance
- Cons
Importance of Centrifugal Pump Technology
Centrifugal pump technology plays a crucial role in numerous industries, including manufacturing, agriculture, mining, and more. These pumps are an essential component in infrastructure development, particularly in water supply systems. They contribute significantly to energy efficiency by optimizing fluid transportation processes. Moreover, centrifugal pump technology aids in maintaining environmental sustainability through wastewater treatment solutions. It facilitates smooth operations in HVAC systems, ensuring comfortable indoor environments.
Essential role in numerous industries
Centrifugal pumps are the backbone of various industries due to their ability to efficiently move fluids. In the manufacturing sector, these pumps are used for various applications such as transferring chemicals and liquids during production processes. In agriculture, centrifugal pumps are utilized for irrigation systems that ensure crops receive adequate water supply. The mining industry relies on these pumps for dewatering mines and transporting slurries containing minerals.
Critical component in infrastructure development
Water supply systems are vital for communities and cities worldwide. Centrifugal pump technology is instrumental in pumping water from sources such as rivers or wells into treatment plants where it undergoes purification before reaching households and businesses. Without efficient centrifugal pumps, the delivery of clean drinking water would be compromised.
Contributes to energy efficiency
Optimizing fluid transportation processes is key to achieving energy efficiency goals. Centrifugal pumps play a significant role by efficiently moving fluids with minimal energy consumption. These pumps are designed with high pump efficiency, allowing them to transfer large volumes of liquid with minimal power requirements. By reducing energy consumption during fluid transportation, centrifugal pump technology contributes to overall energy conservation efforts.
Aids in maintaining environmental sustainability
Wastewater treatment is crucial for preserving our environment and safeguarding public health. Centrifugal pump technology plays a vital role in wastewater treatment plants by facilitating the movement of wastewater through various stages of treatment processes. These pumps help transport wastewater containing contaminants such as chemicals and solids for treatment, ensuring clean water is released back into the environment.
Facilitates smooth operations in HVAC systems
Heating, ventilation, and air conditioning (HVAC) systems are essential for maintaining comfortable indoor environments. Centrifugal pumps are integral components of HVAC systems, responsible for circulating chilled or hot water throughout the building. These pumps ensure that the desired temperature is maintained by efficiently distributing conditioned air. Without reliable centrifugal pump technology, HVAC systems would struggle to provide optimal comfort levels.
In chemical processing industries, centrifugal pumps play a critical role in handling various chemicals and fluids. These pumps are designed to withstand corrosive substances and high-pressure conditions commonly encountered in chemical processes. By efficiently transferring chemicals from one stage to another, centrifugal pump technology enables smooth and safe chemical production.
To summarize, centrifugal pump technology plays a vital role in multiple industries and infrastructure development projects. It contributes to energy efficiency by optimizing fluid transportation processes while aiding in environmental sustainability through wastewater treatment solutions. These pumps facilitate smooth operations in HVAC systems to ensure comfortable indoor environments. The importance of centrifugal pump technology cannot be overstatedConserving energy resources, and promoting sustainable practices across various sectors.
Advantages and Disadvantages of Centrifugal Pumps
Advantages
Centrifugal pumps offer several advantages over positive displacement pumps. Let's take a closer look at some of these benefits:
Higher flow rates compared to positive displacement pumps
One major advantage of centrifugal pumps is their ability to handle higher flow rates. This means they can move larger volumes of fluid in a given amount of time compared to positive displacement pumps. The design and operation of centrifugal pumps allow for efficient movement of fluids, making them ideal for applications that require high flow rates.
Lower initial costs due to simpler design and construction
Centrifugal pumps are generally more cost-effective than positive displacement pumps. This is because they have a simpler design and construction, which translates into lower manufacturing costs. If you're looking for an affordable pumping solution without compromising on performance, centrifugal pumps are a great option.
Compact size and easy installation in various applications
Another advantage of centrifugal pumps is their compact size and ease of installation. These pumps are designed to be space-efficient, making them suitable for installations where space is limited. The straightforward installation process makes it easier to integrate centrifugal pumps into different applications quickly.
Disadvantages
While there are many advantages to using centrifugal pumps, it's important to consider the potential drawbacks as well. Here are some disadvantages associated with these types of pumps:
Limited suitability for high-viscosity fluids or those with solids content
One limitation of centrifugal pumps is their limited suitability for handling high-viscosity fluids or those with solids content. Due to their design, these types of pump may struggle with thicker liquids or materials that contain solid particles. In such cases, alternative pump solutions like positive displacement pumps may be more appropriate.
Performance affected by changes in system conditions such as pressure fluctuations
Centrifugal pump performance can be affected by changes in system conditions, particularly pressure fluctuations. Variations in pressure can impact the pump's ability to deliver a consistent flow rate. It's important to consider the stability of your system and ensure that any pressure fluctuations are within the acceptable range for centrifugal pumps.
Requires regular maintenance to prevent wear and ensure optimal performance
Like any mechanical equipment, centrifugal pumps require regular maintenance to prevent wear and maintain optimal performance. This includes tasks such as lubrication, checking for leaks, and inspecting impellers for damage or erosion. Neglecting maintenance can lead to decreased efficiency, increased energy costs, and potential breakdowns.
Key Components and Functions in Centrifugal Pumps
We learned how these pumps work by converting rotational energy into kinetic energy to move fluids. There are various types of centrifugal pumps, each designed for specific applications such as irrigation, wastewater treatment, and chemical processing.
Understanding the advantages and benefits of centrifugal pumps is crucial when selecting the right pump for your needs. These pumps offer high efficiency, low maintenance requirements, and a wide range of materials to choose from for compatibility with different fluids. However, it's important to be aware of common problems that may arise with centrifugal pumps and how to troubleshoot them.
To conclude, mastering the technology behind centrifugal pumps opens up a world of possibilities for fluid handling in numerous industries. Whether you're looking to upgrade your existing system or starting from scratch, consider the factors discussed in this blog post to make an informed decision. Remember to reach out to leading manufacturers and suppliers who can provide expert guidance tailored to your specific requirements. Don't hesitate—take control of your fluid handling needs today!
FAQs
What is the typical lifespan of a centrifugal pump?
Centrifugal pump lifespans can vary depending on factors such as operating conditions, maintenance practices, and quality of materials used. However, with proper care and regular maintenance, a well-designed centrifugal pump can last anywhere from 10 to 20 years or more.
Can I use a centrifugal pump for pumping abrasive fluids?
While centrifugal pumps are generally not recommended for pumping highly abrasive fluids due to potential wear on internal components, there are specialized designs available that can handle abrasive materials more effectively. Consider consulting with manufacturers or suppliers who specialize in pumps suitable for abrasive applications.
How do I determine the correct size of a centrifugal pump?
The size of a centrifugal pump depends on several factors including desired flow rate, head pressure, and the characteristics of the fluid being pumped. Consulting with a pump specialist or using online calculators can help you determine the appropriate pump size for your specific application.
Are centrifugal pumps suitable for handling viscous fluids?
Centrifugal pumps are typically better suited for low to medium viscosity fluids.Positive displacement pumps may be more efficient and effective in maintaining flow rates.
What maintenance is required for centrifugal pumps?
Regular maintenance is essential to ensure optimal performance and longevity of centrifugal pumps. This includes inspecting and cleaning the impeller, checking alignment, monitoring vibration levels, lubricating bearings, and replacing worn-out parts as needed. It's recommended to follow the manufacturer's guidelines for specific maintenance procedures.