22 Oct 2023
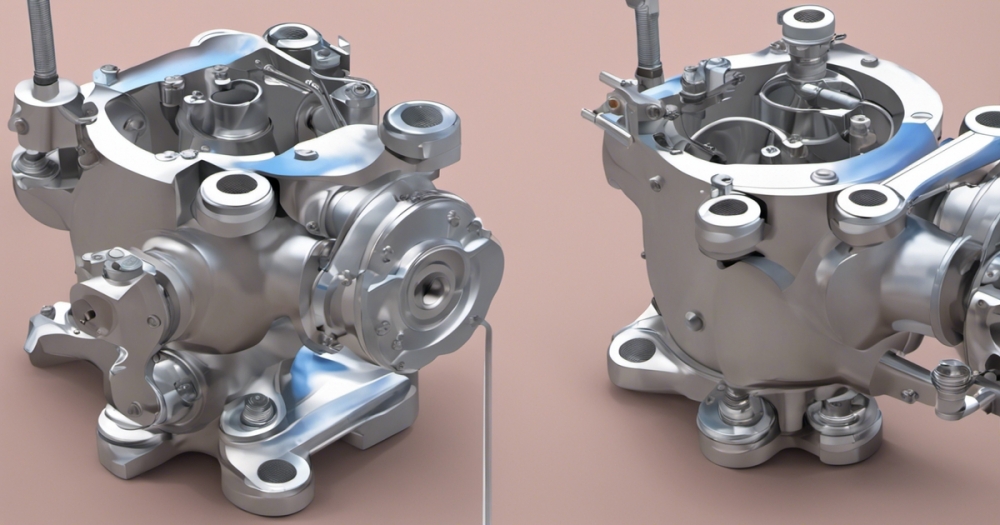
Diaphragm Pump: Unveiling the Working Principle
Diaphragm Pump: Unveiling the Working Principle
The flexible diaphragm pump is a versatile and efficient pumping solution that utilizes compressed air to operate. It is commonly equipped with a ball valve or air valve, making it suitable for a wide range of industries and applications. The positive displacement pump utilizes a flexible diaphragm to transfer fluids, offering reliable performance and a long service life. It is also known as a membrane pump or ball valve series pump. With its unique design, the flexible diaphragms in the diaphragm pump ensure smooth and consistent fluid flow, making it an ideal choice for both high-pressure and low-pressure applications. The diaphragm pump is especially effective when used with a ball valve or air valve, as it can efficiently handle compressed air.
One of the key advantages of the diaphragm pump is its ability to handle different types of fluids, including corrosive and abrasive substances. This makes it an ideal product for various applications that require efficient fluid transfer, such as in the food and beverage industry where CIP (clean-in-place) processes are essential. The diaphragm pump's air valve technology ensures smooth and reliable operation, even in challenging environments or high-pressure zones. This makes the positive displacement pump suitable for a wide range of industries such as chemical processing, mining, wastewater treatment, and food processing. The product is commonly used in these industries due to its efficiency and reliability. Double diaphragm pumps and membrane pumps are popular types of positive displacement pumps that are widely utilized in various applications. The double diaphragm pump, a reliable and efficient product, consists of two diaphragms working in tandem with ball valves. This enhances efficiency and reliability, making it a popular choice for many industries. The pump's unique design ensures that the number of CIP cycles can be maximized, further improving its performance.
Join us as we explore the world of diaphragm pumps and learn why they are an essential product in fluid transfer processes. Discover the reasons why a large number of industries rely on diaphragm pumps for their fluid transfer needs.
Components and Mechanisms of a Diaphragm Pump
A diaphragm pump, also known as a membrane pump, is a product that consists of several essential components that work together to facilitate the pumping process. The product operates by utilizing a number of key mechanisms to ensure efficient pumping. These components include an inlet valve, outlet valve, diaphragm, drive mechanism, and series pump product number. Let's delve into each one in more detail.
Inlet Valve
The inlet valve is responsible for allowing the fluid to enter the double diaphragm pump product. It ensures that the desired diaphragm number is achieved. Double diaphragm pumps are a product that opens when the pressure on the inlet side is lower than that on the outlet side, creating a pressure differential. This is determined by the diaphragm number. This allows the liquid to flow into the double diaphragm pump chamber, increasing the product's efficiency.
Outlet Valve
On the other hand, we have the outlet valve of the double diaphragm pumps which controls the flow of fluid out of the product. The diaphragm number is an important factor to consider when selecting a pump. The outlet valve of double diaphragm pumps opens when there is a higher pressure on the outlet side compared to the inlet side. This depends on the diaphragm number. This ensures that once pumped, fluids can only move in one direction - out of the double diaphragm pumps. The diaphragm number determines this.
Diaphragm
The diaphragm plays a crucial role in separating two chambers within the pump: the liquid chamber and air chamber. Made from flexible material such as rubber or thermoplastic elastomer, double diaphragm pumps create a seal between these two chambers. The diaphragm number plays a crucial role in the functionality of these pumps. As the double diaphragm pumps move back and forth due to reciprocating motion controlled by the drive mechanism, they alternately pressurize and depressurize each chamber, depending on the diaphragm number.
Drive Mechanism
The drive mechanism controls and powers the reciprocating motion of the diaphragm. It can be driven by various means such as an electric motor or pneumatic system. When power is applied to this mechanism, it causes movement in either direction, pushing or pulling on one side of the diaphragm while releasing pressure on its opposite side.
With each stroke of reciprocation initiated by this mechanism, fluids are drawn into one chamber while being expelled from another. This continuous alternating action enables efficient pumping without any need for rotating parts.
Valves
Both inlet and outlet valves are crucial for the proper functioning of a diaphragm pump. These valves ensure that fluids flow in only one direction through the pump, preventing backflow and maintaining an efficient pumping process.
The inlet valve opens when the pressure on the inlet side is lower than that on the outlet side, allowing fluid to enter the pump chamber. Meanwhile, the outlet valve opens when there is higher pressure on the outlet side compared to the inlet side, enabling fluid to be expelled from the pump.
These valves play a vital role in maintaining unidirectional flow and preventing any potential mixing or contamination of fluids being pumped. They are typically designed as check valves or non-return valves to ensure this one-way flow.

Working Principle of Diaphragm Pumps
Reciprocating Action Generates Suction and Discharge
The working principle of diaphragm pumps is based on a reciprocating action that generates suction on one stroke and discharge on the other stroke. This unique mechanism allows for the efficient movement of fluids or gases through the pump.
Flexing Diaphragm Creates Pressure Differentials
At the heart of a diaphragm pump is a flexible diaphragm that flexes back and forth to create pressure differentials. When the diaphragm moves in one direction, it creates suction, drawing in the fluid or gas into the pump chamber. On its return stroke, the diaphragm pushes against the fluid or gas, generating pressure and forcing it out of the pump.
Air or Fluid Pressure Drives Diaphragm Movement
The movement of the diaphragm in a diaphragm pump is driven by either air pressure or fluid pressure. In an air-operated diaphragm pump (AODD), compressed air is used to move the diaphragms back and forth. As air is supplied to one side of the diaphragm, it pushes against it, causing it to flex and create suction or discharge. Similarly, in a hydraulic-operated diaphragm pump (HODD), fluid pressure acts upon one side of the diaphragms to generate movement.
Precise Control Over Flow Rates and Pressures
One significant advantage of using a positive displacement pump like a diaphragm pump is its ability to provide precise control over flow rates and pressures. The reciprocating action ensures that consistent volumes are moved with each stroke, allowing for accurate dosing or metering applications.
Diaphragm pumps offer several benefits due to their working principle:
- Versatility: Diaphragm pumps can handle various types of fluids, including corrosive chemicals, viscous liquids, slurries, and even solids-laden liquids. This versatility makes them suitable for a wide range of industries, such as chemical processing, wastewater treatment, food and beverage, and pharmaceuticals.
- Self-Priming: Diaphragm pumps are self-priming, meaning they can draw fluid into the pump without the need for external priming. This feature eliminates the hassle of manually priming the pump before each use.
- Dry Run Capability: Unlike some other pump types, diaphragm pumps can run dry without suffering damage. This is particularly useful in applications where there may be intermittent flow or when the pump needs to be shut down temporarily.
- No Contamination: The diaphragm acts as a barrier between the pumped fluid or gas and the driving mechanism. As a result, there is no risk of contamination or leakage from lubricants or seals into the process stream.
Advantages of Diaphragm Pumps
Diaphragm pumps offer several advantages that make them a popular choice for various applications. Let's explore some of the key benefits of using diaphragm pumps:
Ability to handle abrasive, viscous, corrosive, or shear-sensitive fluids
One of the major advantages of diaphragm pumps is their ability to handle a wide range of fluids. Whether it's abrasive materials, viscous liquids, corrosive chemicals, or shear-sensitive substances, diaphragm pumps can effectively pump and transfer these fluids without any issues. This versatility makes them highly suitable for industries such as mining, chemical processing, wastewater treatment, and food processing.
- Diaphragm pumps are capable of handling abrasive fluids such as slurries and sludges without causing damage to the pump itself.
- They can efficiently handle high-viscosity liquids like adhesives and paints without clogging or reducing performance.
- Corrosive chemicals that would corrode other types of pumps can be safely handled by diaphragm pumps due to their corrosion-resistant materials.
- Shear-sensitive fluids like pharmaceuticals and delicate emulsions can be pumped gently without compromising their integrity.
Self-prime capabilities eliminate the need for external priming systems
Another advantage of diaphragm pumps is their self-priming capability. Unlike some other pump types that require external priming systems or manual priming before operation, diaphragm pumps can automatically prime themselves. This feature saves time and effort during setup and eliminates the need for additional equipment.
- Diaphragm pumps have a suction stroke that creates a vacuum effect within the pump chamber, allowing them to draw in fluid from the source without any external assistance.
- The self-priming capability makes diaphragm pumps ideal for applications where continuous pumping is required or when dealing with intermittent flow conditions.
Can run dry without damage due to their positive displacement design
Diaphragm pumps are designed with a positive displacement mechanism, which means they can operate without fluid present. This feature allows them to run dry for extended periods without causing any damage to the pump. This is particularly useful in situations where there may be fluctuations in fluid supply or when occasional dry running is unavoidable.
- The positive displacement design of diaphragm pumps ensures that a fixed volume of fluid is displaced with each stroke, regardless of whether there is actual fluid present.
- This design characteristic prevents overheating and mechanical wear that could occur if the pump were to run continuously without any liquid.
Offer leak-free operation with no risk of contamination or product loss
Diaphragm pumps provide leak-free operation, ensuring that fluids are transferred without any risk of leakage or contamination. The diaphragm acts as a barrier between the pumped fluid and the environment, preventing any cross-contamination or loss of valuable products.
- The diaphragm separates the liquid chamber from the air side, creating a reliable seal that prevents leaks.
- This feature makes diaphragm pumps suitable for applications where hygiene and cleanliness are crucial, such as in pharmaceutical manufacturing or food processing industries.
- Diaphragm pumps also eliminate the need for additional sealing mechanisms like mechanical seals or gland packing, reducing maintenance requirements and potential points of failure.
Applications of Diaphragm Pumps
Diaphragm pumps are versatile and find extensive use in various industries due to their unique capabilities. Let's explore some of the common applications where diaphragm pumps excel:
Widely used in chemical processing, pharmaceuticals, food & beverage industries
Diaphragm pumps are highly valued in industries such as chemical processing, pharmaceuticals, and food & beverage. In chemical processing plants, these pumps are invaluable for transferring corrosive acids, solvents, adhesives, and other aggressive chemicals. Their ability to handle a wide range of fluids makes them an ideal choice.
Similarly, in the pharmaceutical industry, diaphragm pumps play a crucial role in the production process. They are used for transferring liquids with high precision and maintaining sterile conditions. These pumps ensure that sensitive medications and ingredients are handled carefully without any contamination.
The food and beverage industry also benefits from diaphragm pumps' versatility. These pumps can handle various substances like fruit juices, sauces, dairy products, and even viscous materials like chocolate or honey. The ability to pump such diverse fluids makes diaphragm pumps indispensable in this sector.
Ideal for transferring acids, solvents, adhesives, sludge, wastewater etc.
One of the major advantages of diaphragm pumps is their ability to handle a wide range of fluids effectively. They excel at transferring corrosive acids commonly found in industrial settings while maintaining safety standards. Diaphragm pumps can also handle volatile solvents without any risk of leakage or contamination.
Moreover, these pumps prove valuable when dealing with challenging substances such as adhesives or sludge. The robust construction of diaphragm pumps allows them to handle thick or sticky materials efficiently without clogging or damage.
In addition to handling chemicals and viscous substances, diaphragm pumps are also suitable for pumping wastewater. They can effectively move dirty water containing solids without any issues. This makes them an excellent choice for wastewater treatment facilities or any application that involves the transfer of slurry or sewage.
Commonly employed in paint spraying equipment and printing presses
Diaphragm pumps play a vital role in industries that require precise and controlled fluid delivery, such as paint spraying equipment and printing presses. In paint spraying applications, diaphragm pumps provide consistent pressure and flow rate, ensuring an even coat of paint on surfaces. They are also capable of handling different types of paints, including those with high viscosity.
Similarly, in the printing industry, diaphragm pumps are essential for ink transfer. These pumps deliver ink to the printing plates with accuracy and reliability. The ability to handle various types of inks makes them suitable for different printing processes like offset, flexography, or gravure.
Used in medical devices such as blood analyzers or dialysis machines
The medical field relies on diaphragm pumps for critical applications within devices like blood analyzers or dialysis machines. Diaphragm pumps ensure precise fluid control during blood analysis by accurately delivering reagents and samples. This level of accuracy is crucial for obtaining accurate test results.
In dialysis machines, diaphragm pumps help remove waste products from the patient's bloodstream while maintaining proper fluid balance. These pumps ensure the safe and efficient filtration process required for patients undergoing dialysis treatment.
Verderair Diaphragm Pump: Features and Specifications
Constructed with Durable Materials
The Verderair diaphragm pump is built to last, thanks to its construction using durable materials such as stainless steel or polypropylene. These materials ensure that the pump can withstand the rigors of various applications without succumbing to corrosion or wear and tear.
Wide Variety of Sizes and Flow Rates
One of the standout features of the Verderair diaphragm pump is its versatility in terms of size and flow rate options. With a wide variety of sizes available, ranging from small compact models to larger industrial-grade pumps, there is a suitable option for every application. These pumps offer flow rates ranging from 1 to 1500 liters per minute, catering to different pumping requirements.
Handling Aggressive Chemicals, High Viscosity Fluids, and Solids
The Verderair diaphragm pump is designed to handle even the most challenging substances. Whether it's aggressive chemicals, high viscosity fluids, or solids suspended in liquid form, this pump can tackle them all with ease. Its robust construction ensures that it can withstand the demands of pumping corrosive or abrasive substances without compromising performance.
Air-Operated or Electric-Driven Models
Another notable feature of the Verderair diaphragm pump is its flexibility in terms of operation. It offers options for both air-operated and electric-driven models, allowing users to choose the power source that best suits their needs. The air-operated versions are particularly advantageous in environments where electricity may not be readily available or where safety considerations come into play.
Installation and Benefits of Double Diaphragm Pump
Easy installation with minimal maintenance requirements
Installing a double diaphragm pump is a breeze, requiring minimal effort and time. With its simple design and user-friendly features, it can be easily integrated into any system or setup. Unlike other pumps that may require complex installation procedures or specialized tools, the double diaphragm pump offers convenience and efficiency.
Maintenance is also hassle-free with this type of pump. Its modular construction allows for easy access to individual components, making repairs and replacements quick and straightforward. This means less downtime for your operations and more productivity in the long run.
Can handle abrasive, viscous, and volatile fluids effectively
One of the standout benefits of a double diaphragm pump is its ability to handle a wide range of fluids effectively. Whether you're dealing with abrasive liquids, highly viscous substances, or volatile chemicals, this pump can handle them all with ease.
The robust construction of the double diaphragm pump ensures durability even when pumping aggressive or corrosive fluids. The diaphragms are made from tough materials such as Teflon or Santoprene®, which provide excellent resistance against wear and tear. This makes it suitable for use in various industries including chemical processing, mining, wastewater treatment, food processing, and more.
Provides redundancy with two diaphragms for added reliability
Reliability is crucial. The double diaphragm pump offers an added layer of security with its redundant design featuring two diaphragms working in tandem.
In case one diaphragm fails due to damage or wear over time, the second diaphragm takes over seamlessly without interrupting the operation. This redundancy feature ensures continuous pumping without any downtime or loss in productivity. It provides peace of mind knowing that your system will keep running smoothly even if one component encounters an issue.
Enables continuous operation even if one diaphragm fails
The ability to maintain continuous operation is a significant advantage of the double diaphragm pump. In situations where a single diaphragm pump would require immediate shutdown for repairs or replacement, the double diaphragm pump keeps going.
This uninterrupted operation is crucial in industries where downtime can result in significant financial losses. With a double diaphragm pump, you can avoid costly delays and keep your operations running smoothly. It provides a reliable solution for applications that demand continuous pumping without any interruptions.
Harnessing the Power of Diaphragm Pumps
The previous sections have provided a comprehensive understanding of diaphragm pumps, their components, working principles, advantages, applications, and specific features of the Verderair Diaphragm Pump. These versatile pumps offer a reliable solution for various industries and applications that require efficient fluid transfer. With their ability to handle both corrosive and abrasive fluids, diaphragm pumps ensure optimal performance and longevity.
To maximize the benefits of diaphragm pumps in your operations, it is crucial to consider factors such as installation requirements and the advantages offered by double diaphragm pumps. By following proper installation procedures and utilizing double diaphragm pump technology, you can enhance efficiency while minimizing downtime.
As you explore the world of diaphragm pumps further, we encourage you to delve into more detail-oriented responses regarding your specific needs. Understanding factors such as flow rates, material compatibility, pressure capabilities, and maintenance requirements will help you make an informed decision when selecting a diaphragm pump for your application. Embrace the power of diaphragm pumps today and experience their reliability in achieving seamless fluid transfer.
FAQs
What are the main components of a diaphragm pump?
A diaphragm pump consists of several key components including an air valve system, check valves (inlet and outlet), a drive mechanism (pneumatic or hydraulic), a flexible diaphragm made from materials like rubber or thermoplastics, and liquid chambers.
Can I use a diaphragm pump for abrasive fluids?
Yes! One advantage of using a diaphragm pump is its ability to handle abrasive fluids with ease. The flexible nature of the diaphragms allows them to withstand wear caused by particles in the fluid being pumped.
Are there any maintenance requirements for diaphragm pumps?
Diaphragm pumps generally require minimal maintenance compared to other types of pumps. However, regular inspections should be conducted to ensure proper functioning of the diaphragms, check valves, and seals. It is also important to follow manufacturer guidelines for lubrication and replacement intervals.
Can diaphragm pumps handle corrosive fluids?
Yes, diaphragm pumps are suitable for handling corrosive fluids. The choice of materials used in the construction of the pump, such as stainless steel or chemically resistant thermoplastics, ensures compatibility with a wide range of corrosive substances.
What are the advantages of using a double diaphragm pump?
Double diaphragm pumps offer enhanced performance by providing redundancy and increased flow rates. They also allow for continuous operation even if one side fails, reducing downtime and ensuring uninterrupted fluid transfer.